Heat Distribution in Powder Coating Ovens
4 min read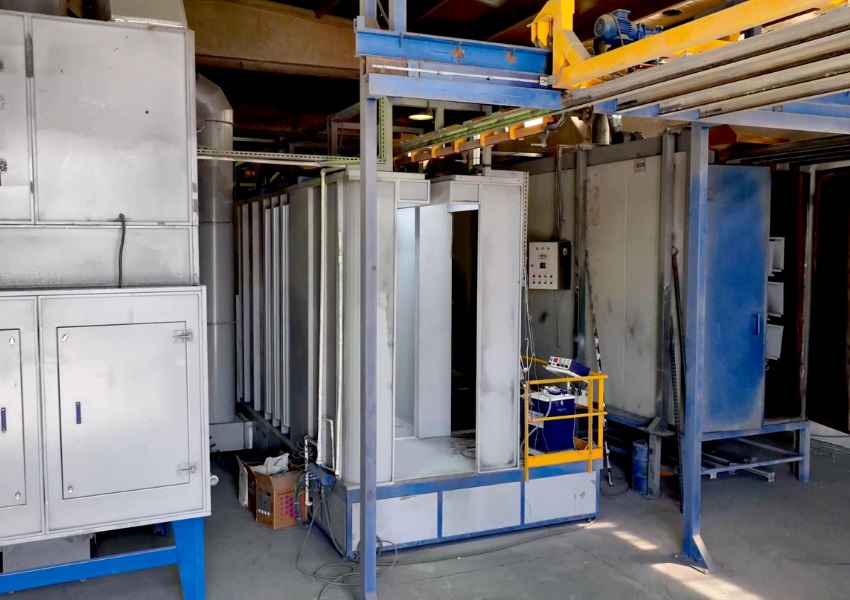
Last Updated on September 15, 2024 by MrHudson
When it comes to achieving that flawless finish in powder coating, heat distribution is the secret sauce that makes it all happen. Powder coating ovens are marvels of engineering, designed to apply just the right amount of heat to ensure a perfect coat. But what really goes on inside these ovens? How does heat flow, and what factors play a role in ensuring that every corner of the object being coated receives uniform heat? Let’s dive into the science behind heat distribution in powder-coating ovens and uncover what makes these machines tick.
Understanding the Principles of Heat Flow in Powder Coating Ovens
At the heart of every powder-coating oven lies the principle of heat flow. Heat naturally moves from hotter areas to cooler areas, a process known as heat transfer. In powder coating ovens, this heat transfer must be carefully managed to ensure that the coating cures evenly across the entire surface of the object. The aim is to avoid any areas being too hot or too cold, which can result in uneven curing and an unsatisfactory finish.
The process begins with heating elements, usually located at strategic points within the oven. These elements generate the necessary heat, which is then distributed throughout the oven chamber. The challenge lies in making sure this heat reaches every part of the object evenly. Factors such as the size of the oven, the placement of heating elements, and the airflow all play crucial roles in determining how heat flows within the powder-coating oven.
The Role of Convection in Achieving Even Heat Distribution
Convection is the unsung hero in the world of heat distribution. In powder-coating ovens, convection refers to the movement of heat through the air, driven by the circulation of hot and cold air within the oven chamber. This movement ensures that heat is spread evenly, reducing the risk of hot spots or cold spots that could affect the quality of the coating.
In a powder coating oven, fans or blowers are often used to promote convection, circulating the air and helping to distribute heat more uniformly. This is especially important when coating large or complex objects, where certain areas might otherwise be shielded from direct heat. By enhancing convection, the oven can maintain a consistent temperature throughout the chamber, ensuring that every inch of the object being coated is exposed to the right amount of heat for the right amount of time.
How Oven Design Influences Heat Distribution Patterns
The design of a powder coating oven is more than just a box with heating elements—it’s a carefully engineered system where every component plays a role in heat distribution. The shape and size of the oven, the placement of heating elements, and the design of the airflow system all contribute to how heat is distributed within the chamber.
For instance, in some powder-coating ovens, the heating elements are placed along the sides or bottom of the chamber to encourage heat to rise and circulate naturally. In others, a more centralized design might be used, with heat being introduced at specific points to create a more controlled flow. The goal is to create a heat distribution pattern that ensures uniform exposure, regardless of the shape or size of the object being coated.
The design also considers the door placement and sealing mechanisms, as even the smallest gap or draft can lead to uneven heat distribution. By meticulously designing every aspect of the oven, manufacturers ensure that their powder-coating ovens deliver consistent and reliable results.
The Impact of Insulation on Maintaining Consistent Temperatures
Insulation might not be the most glamorous aspect of a powder-coating oven, but it plays a critical role in maintaining consistent temperatures. Good insulation keeps the heat where it belongs—inside the oven—preventing energy loss and ensuring that the temperature remains stable throughout the coating process.
In powder-coating ovens, insulation is typically made from materials that can withstand high temperatures while minimizing heat transfer to the outside environment. This not only improves the efficiency of the oven by reducing energy consumption but also contributes to more even heat distribution. When the oven’s temperature is consistent, the risk of uneven curing is significantly reduced, leading to a better-quality finish.
Moreover, insulation helps in protecting the external environment from the intense heat generated within the oven. This is particularly important in industrial settings, where safety and energy efficiency are paramount. High-quality insulation ensures that the oven operates efficiently, maintaining the desired temperature with minimal fluctuations, which is key to achieving a perfect powder coat.
Measuring and Monitoring Heat Distribution for Optimal Coating Results
To achieve optimal results in powder coating, it’s not enough to simply assume that the heat is evenly distributed—you need to measure and monitor it. Modern powder coating ovens are equipped with advanced sensors and monitoring systems that provide real-time data on temperature distribution within the chamber. This information is crucial for making adjustments on the fly and ensuring that the coating process goes smoothly.
These sensors can detect even minor temperature variations, allowing operators to make precise adjustments to the heating elements or airflow to correct any inconsistencies. By continuously monitoring the heat distribution, operators can ensure that the coating is applied evenly and that the final product meets the highest quality standards.